Blog
How to Inspect a Used Injection Moulding Machine Before Buying
Apr 16, 2025
Andrea Balajová
Purchasing a used injection moulding machine can be a smart, cost-effective decision for manufacturers looking to expand capacity or reduce capital expenditure. However, to ensure a safe investment, it’s essential to carry out a thorough inspection of the machine before finalizing the purchase. In this guide, we’ll walk you through the key areas to inspect, what to look out for, and how to evaluate the machine’s condition to avoid surprises after delivery. 1. START WITH DOCUMENTATION AND SERVICE HISTORY Before you physically inspect the machine, ask the seller or dealer for the following: • Complete service records (maintenance intervals, repairs, upgrades) • Original technical documentation (manuals, wiring diagrams, CE certificates) • Previous usage details (type of production, operating hours, material used) A well-documented machine typically indicates that it was maintained properly, and knowing its background helps anticipate potential wear or replacement needs. 2. VISUAL CONDITION: FIRST IMPRESSIONS MATTER Begin with a visual check of the entire machine: • Are there signs of corrosion, oil leaks, or damaged components? • Is the paint original or recently reapplied to hide wear? • Are the tie bars straight and free from scoring? • Are safety guards and covers intact? While cosmetic flaws aren’t always critical, they may suggest how the machine was treated during its lifetime. 3. CHECK THE CLAMPING UNIT The clamping unit undergoes high mechanical stress and must be in good working order. Inspect the following: • Tie bars and platens for wear, cracks, or deformation • Hydraulic cylinders for leaks or inconsistent movement • Toggle or direct-locking system for smooth operation • Lubrication points and whether the system works automatically and consistently Ask to measure the parallelism of the platens — misalignment can damage moulds and affect part quality. 4. INSPECT THE INJECTION UNIT This is the heart of the machine, and small issues here can become costly. Check: • Screw and barrel for wear (look for signs of abrasion, corrosion, or low compression) • Nozzle condition and proper heating • Heaters and thermocouples for consistent temperature control • Check valve function and seal • Plasticizing capacity — is it still within acceptable performance range? If possible, ask to perform a screw recovery or injection cycle and watch for inconsistencies. 5. EVALUATE THE HYDRAULIC AND ELECTRICAL SYSTEMS These systems are complex and should be tested thoroughly. Hydraulic system: • Look for fluid leaks, hose wear, and pump noise • Check pressure settings and response times • Inspect cooling system and filters Electrical system: • Test the control unit (often a brand’s proprietary system like Arburg Selogica or Engel CC300) • Check for fault messages, sensor feedback, and interface responsiveness • Ensure all safety interlocks and emergency stop functions are working properly 6. CONTROL SYSTEM AND SOFTWARE The PLC control is the brain of the machine. An outdated or failing control system can lead to serious operational issues. Check for: • Boot-up times and system responsiveness • Touchscreen or keypad functionality • Backup and restore options for machine settings • Availability of software updates or support from the OEM Older controls may still be functional but harder to service or source parts for. 7. RUN THE MACHINE IF POSSIBLE If the machine is still connected, request a test run under real or simulated production conditions. Watch for: • Startup sequence and cycle time • Pressure and temperature consistency • Alarms, vibrations, or abnormal sounds • Part quality (if mould and material are available) A live test gives you the clearest picture of machine health. 8. ASK FOR A THIRD-PARTY OR DEALER INSPECTION If you’re not experienced in machine assessment, consider hiring an independent technician or request a dealer inspection report. At BASTA Machines, we thoroughly inspect and document every machine before listing it for sale — including photos, videos, and condition reports. 9. CONSIDER SPARE PARTS AND OEM SUPPORT Check: • Is the machine from a major brand (e.g. Arburg, Engel, Demag, Haitian)? • Are spare parts readily available? • Is technical support still offered by the manufacturer? Machines from well-known brands usually offer longer service life thanks to easier sourcing of components. Final Thoughts Inspecting a used injection moulding machine doesn’t require advanced tools — just a sharp eye, a checklist, and a bit of knowledge. With a proper inspection, you reduce risk, increase confidence, and get more value from your investment. Want to see an example inspection? Check out our helpful videos on YouTube or see our machines working: • Injection moulding test run [https://www.youtube.com/shorts/943vMdId4Ys] Or get in touch with us at www.bastamachines.com [http://www.bastamachines.com] — our team is happy to help you choose and inspect the right machine for your needs.
Read article
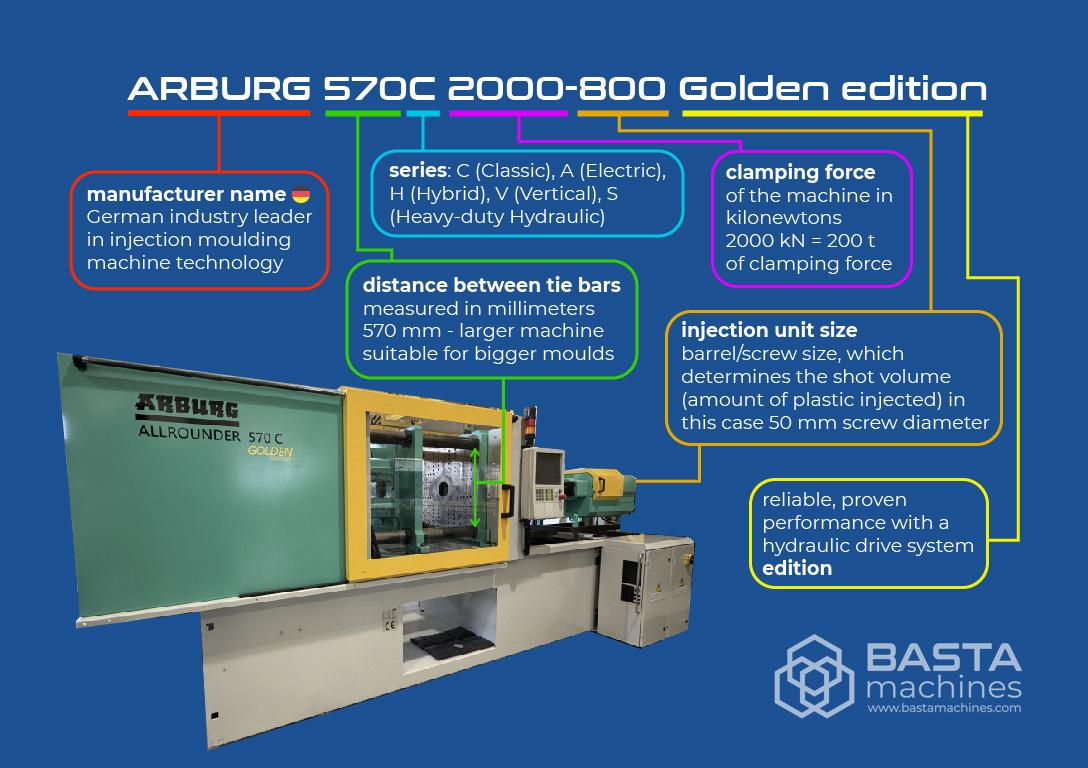
How to Read Injection Moulding Machine Model Numbers: A Beginner’s Guide
Apr 14, 2025
Andrea Balajová
If you’re browsing used injection moulding machines, you’ve probably come across listings with model numbers like ENGEL Victory 330/80 Tech, Arburg Allrounder 470C 1000-290, or Demag Ergotech 500-2000 System. While these combinations of numbers and letters might seem cryptic at first, they actually follow specific naming conventions that provide valuable information about the machine’s capabilities. In this beginner’s guide, we’ll show you how to decode injection moulding machine model numbers so you can make more informed decisions when buying. 1. WHY MODEL NUMBERS MATTER Model numbers aren’t random. They typically include data about: • Clamping force • Screw diameter • Machine series or generation • Optional features or technologies Understanding what each part of the model number represents helps you quickly identify whether the machine matches your production needs — without diving deep into full technical specs. 2. BREAKING DOWN COMMON MODEL NUMBER FORMATS BY BRAND Let’s look at how some of the most popular brands format their model numbers: ARBURG EXAMPLE: ALLROUNDER 470C 1000-290 • 470C – Refers to the distance between tie bars or size of the clamping unit (470 mm) • 1000 – The clamping force in kilonewtons → 1000 kN = 100 tons • 290 – The injection unit size (Arburg’s internal code — usually corresponds to a screw diameter of approx. 30 mm - this affects the shot volume and plasticizing capacity of the machine) So this machine has a 100-ton clamping force. ENGEL EXAMPLE: VICTORY 330/80 TECH • 330 – The screw diameter or shot size (depending on series) • 80 – The clamping force in tons • Victory – Refers to the machine series (toggle-free clamping system) • Tech – Indicates a special version or control system Note: ENGEL’s naming may vary depending on regional markets and series, but clamping force and shot size are almost always present. DEMAG EXAMPLE: ERGOTECH 500-2000 SYSTEM • 500 – The clamping force in kN → 500 kN = 50 tons • 2000 – The screw injection pressure unit or size of the injection unit • System – Indicates control system or configuration Demag machines are typically labeled with the clamping unit first, then the injection unit. 3. OTHER IMPORTANT ABBREVIATIONS AND TERMS Many brands use additional abbreviations or suffixes that reflect machine features: • U – Universal or multi-purpose • T – Tie-barless design • H – Hydraulic • E – Electric • V – Vertical (clamping or injection) • C – Compact or classic design • S – Servo-driven • 2K – Multicomponent Example: Arburg 420S 800-350 V → Vertical version, 80 tons clamping force, 35 mm screw 4. WHY THIS MATTERS WHEN BUYING USED MACHINES Used injection moulding machines are often listed only by model name and year. Knowing how to read the model number helps you: • Filter out machines that don’t meet your tonnage or size requirements • Avoid overpaying for a machine that’s too powerful for your product • Communicate clearly with sellers and brokers • Choose the right combination of clamping and injection units At BASTA Machines, we always provide full model names and technical specifications, but understanding how to decode them gives you an edge as a buyer. 5. NEED HELP MATCHING THE RIGHT MACHINE? If you’re unsure how to interpret a specific model or want advice on selecting the right injection moulding machine for your application, our team is here to help. With years of experience in the used machinery market, we can guide you toward the most efficient and cost-effective solution. Contact us at www.bastamachines.com [http://www.bastamachines.com] — and let us help you find the right machine, not just any machine.
Read article
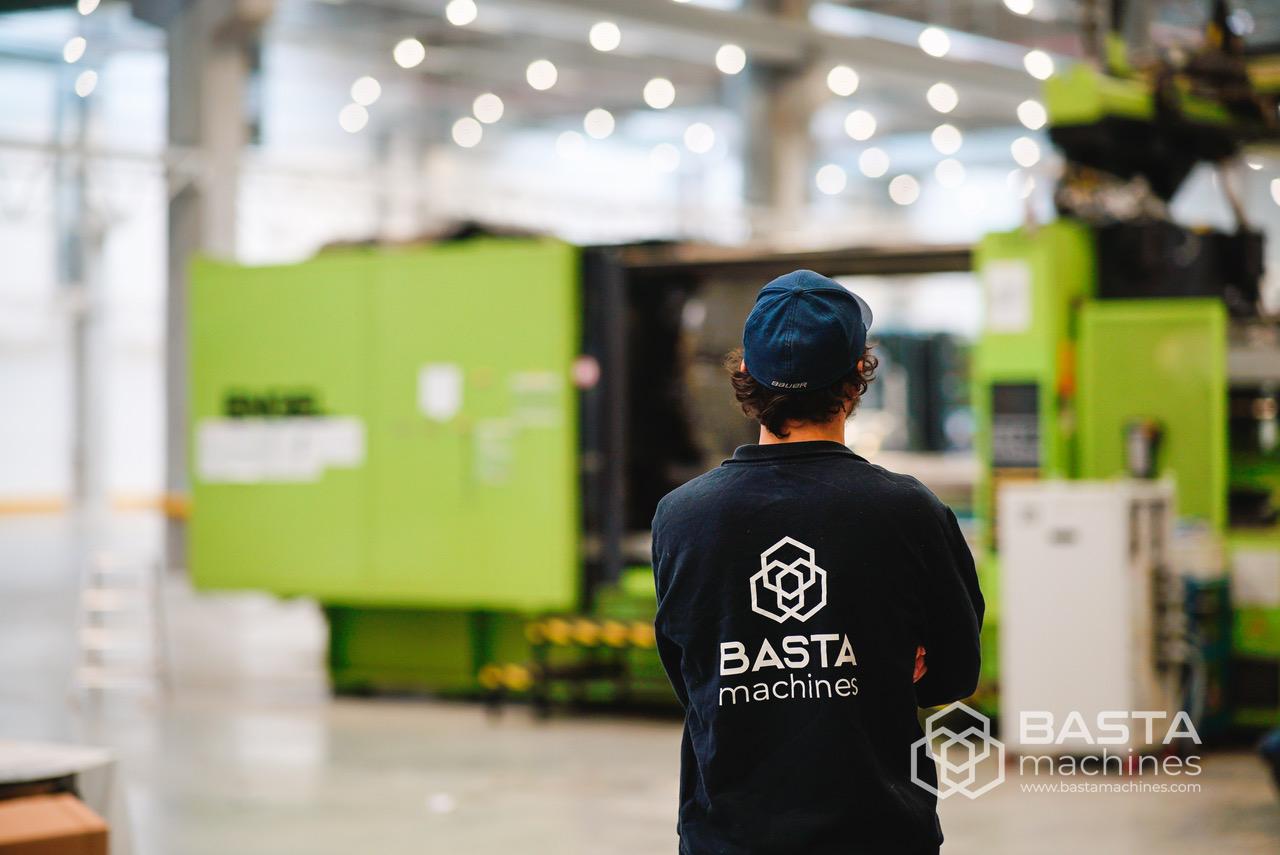
7 Reasons to Buy a Used Injection Moulding Machine
Apr 7, 2025
Andrea Balajová
In the world of plastic manufacturing, injection moulding machines are the backbone of efficient and precise production. These powerful systems are responsible for creating everything from automotive parts and packaging components to electronics housings and medical devices. When investing in a machine, many businesses face a key question: Should we buy a new injection moulding machine or opt for a used one? At BASTA Machines, we specialize in high-quality used injection moulding machines, and we believe the answer often leans in favor of going second-hand — especially when done right. Here’s why. 1. SIGNIFICANT COST SAVINGS The most obvious reason? Price. A used injection moulding machine can cost up to 50–70% less than a new one, depending on the age, condition, and brand. These savings can be redirected into molds, automation, or raw materials — all of which directly affect your production capacity and profitability. 2. IMMEDIATE AVAILABILITY New machines often come with lead times ranging from several weeks to even months, depending on the manufacturer. In contrast, used machines are usually in stock and ready to ship. This means less downtime and faster scaling of your production line. 3. TRUSTED BRANDS AND PROVEN PERFORMANCE When buying used, you’re often purchasing equipment from well-known manufacturers like Arburg, Engel, Demag, Haitian, Krauss Maffei, or Wittmann Battenfeld. These machines are built to last — and a unit with a strong service history can still deliver years of reliable output. Plus, many used machines come from European factories with regular maintenance logs and service records, giving you additional peace of mind. 4. FLEXIBILITY FOR STARTUPS AND EXPANDING BUSINESSES Used machines offer a lower barrier to entry, making them ideal for: • New businesses entering the plastics industry • Companies expanding their capabilities with limited capital • Specialized runs or short-term contracts where new investment isn’t justified They also allow you to test production ideas or molds before committing to full-scale, high-cost solutions. 5. ECO-FRIENDLY MANUFACTURING CHOICE Purchasing second-hand equipment is a sustainable decision. By extending the life of existing machinery, you help reduce industrial waste and the environmental impact associated with new machine manufacturing. In industries under increasing pressure to meet environmental targets, this is a smart and responsible move. 6. EASY UPGRADE AND COMPONENT REPLACEMENT Modern injection moulding machines — even older models — are often modular and upgradable. You can easily: • Replace control units with newer PLCs • Add robots or conveyors • Retrofit energy-saving features • Replace wear parts like screws, barrels, and heaters This gives you the performance of a newer machine at a fraction of the cost. 7. PROFESSIONAL GUIDANCE AND SUPPORT FROM SPECIALISTS Buying used doesn’t mean buying blindly. At BASTA Machines, we: • Inspect and clean every machine before listing • Provide detailed technical specs and photos • Help you match the right model to your production needs • Support you with logistics and export documentation With the right partner, buying a used injection moulding machine becomes a strategic business decision, not a compromise. FINAL THOUGHTS While new machines may offer the latest tech and factory warranties, used injection moulding machines offer speed, savings, and flexibility — without sacrificing quality when sourced properly. Whether you’re starting out, expanding your line, or just optimizing budget and output, used machinery can be the key to faster growth. Looking for a reliable, ready-to-run machine? 👉 Explore our stock of used injection moulding machines here [https://www.bastamachines.com/en/machines/c/plastic-machines-2000/s/injection-moulding-2001?sorting=latestAdditions&page=1] or get in touch with our team [https://bastamachines.com/contact].
Read article